Grain, Seeds & Milling
Magnattack® high-intensity magnetic separators are designed to provide unmatched contaminant control in the grain, milling, and seed processing industries. With a focus on safety, quality, and compliance, our separators capture fine metal particles that could compromise product integrity and equipment performance. Built to withstand demanding conditions, Magnattack systems deliver durable, efficient solutions that protect your product, streamline operations, and ensure regulatory compliance—making us the trusted choice for magnetic separation in these industries.
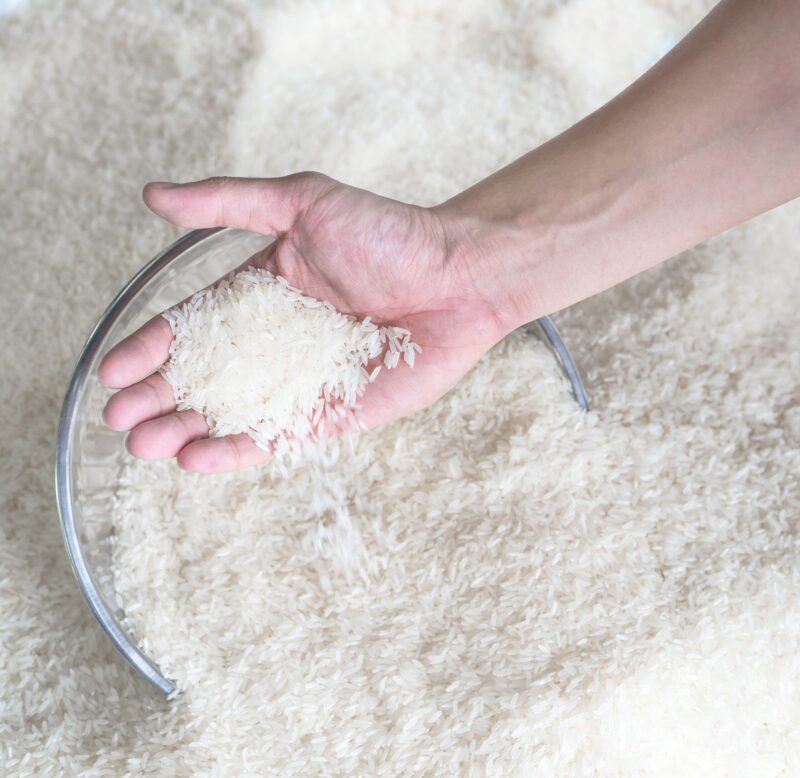
Superior Contaminant Control for Grain, Milling & Seed Processing
In grain, milling, and seed processing, purity, safety, and efficiency are essential. Magnattack® magnetic separators are specifically engineered to tackle the challenges of these industries, delivering reliable metal contaminant control, regulatory compliance, and optimized operation.
Magnattack high-intensity magnetic separators capture and remove fine metal contaminants, such as tramp iron, stainless steel, and ferrous particles, protecting product safety, quality, and equipment functionality. Built from high-strength magnetic materials and food-grade stainless steel, our durable, corrosion-resistant separators meet FDA and HACCP standards, supporting regulatory compliance and ensuring product integrity.
Magnetic separation systems are widely used in milling, grain and seed applications for several key reasons, including the removal of tramp and large metal pieces, prevention of dust explosions caused by metal entering high-impact machinery, protection against damage to high-impact equipment, and increasing product purity and quality. Commonly used magnets in these applications include the Mag-Ram® Self-Cleaning Magnet, Rapidclean® Drawer Magnet, Spherical Inline Pneumatic Transfer Magnet, and various types of Plate Magnets offered by Magnattack.
Optimized for high-volume applications, these separators maintain efficient contaminant control with minimal impact on product flow, reducing equipment wear and maximizing productivity.
With decades of experience and trusted partnerships in grain, milling, and seed processing, Magnattack offers reliable, tailored solutions to enhance product quality, safety, and operational efficiency. Choose Magnattack for effective magnetic separation in your industry.
Markets we work in:
- Bulk Grain Handling & Ship Loading
- Flour, Maize & Rice Milling
- Cereal
- Seeds & Grains
- Stock Feed
USDA Acceptance
Magnattack received a USDA Dairy Acceptance Certification in 2015 for special models of the Mag-Ram® Self Cleaning Separator, Rapidclean® Drawer Magnet, Round Pipe Separator, and the Powder Transfer Magnet. In 2019, the Emulsion & Slurry Pipeline Separator also received the USDA Acceptance Certification for use in dairy and sensitive liquid applications, as well as meat and poultry applications.
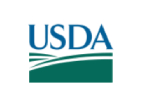
Trusted by Industry Experts
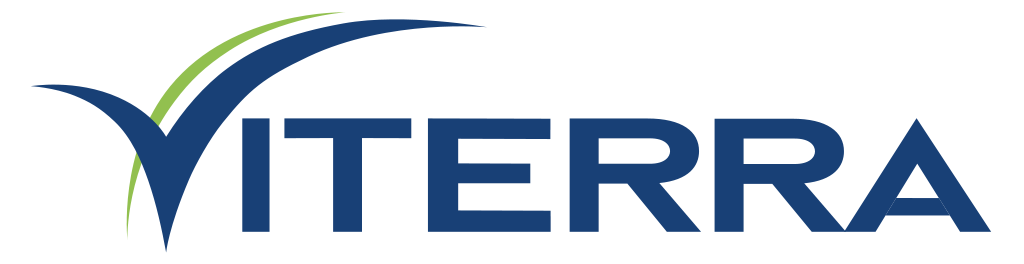
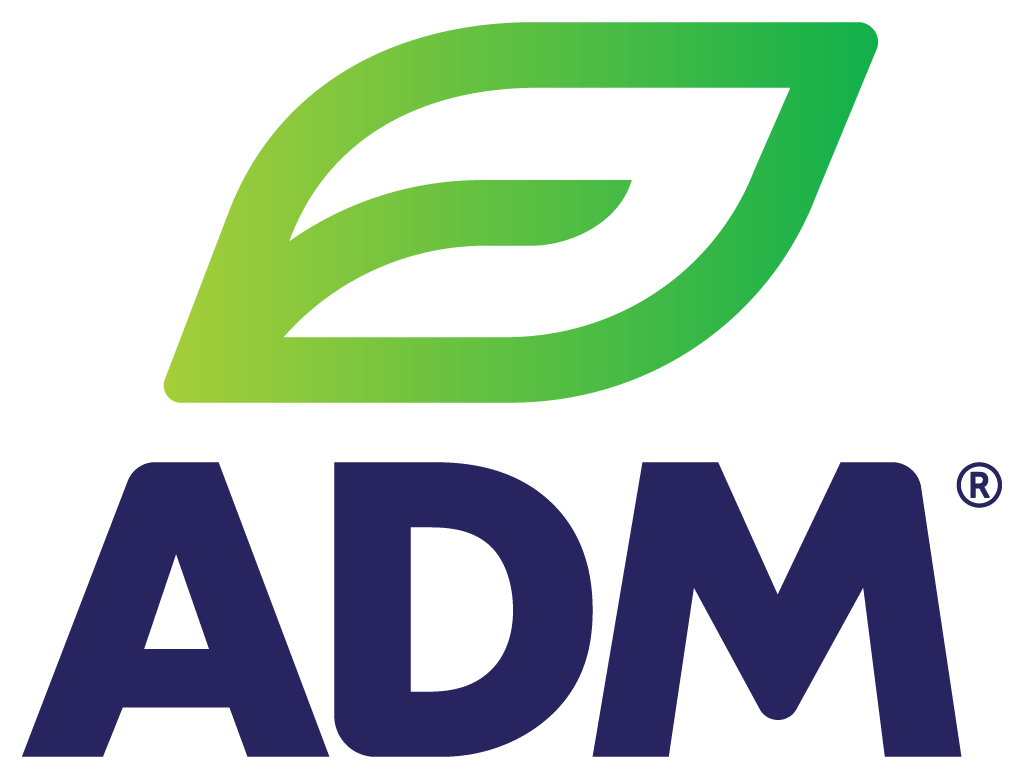
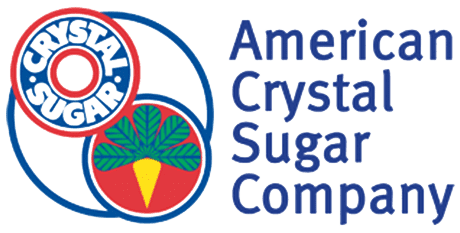
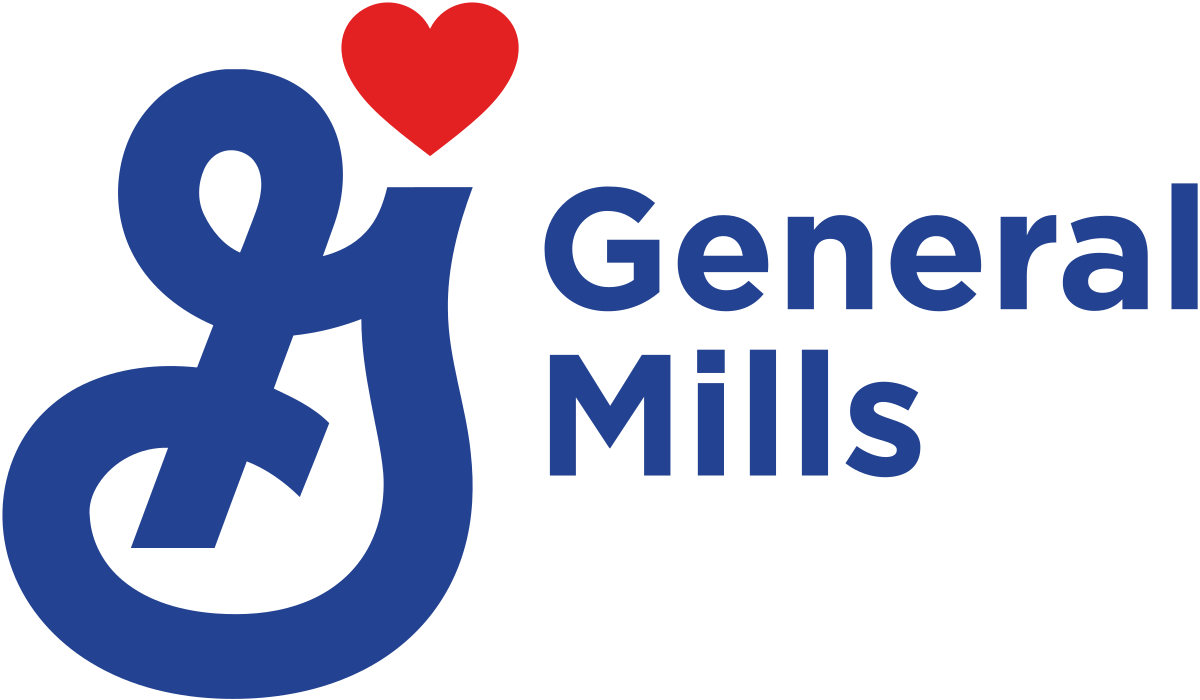
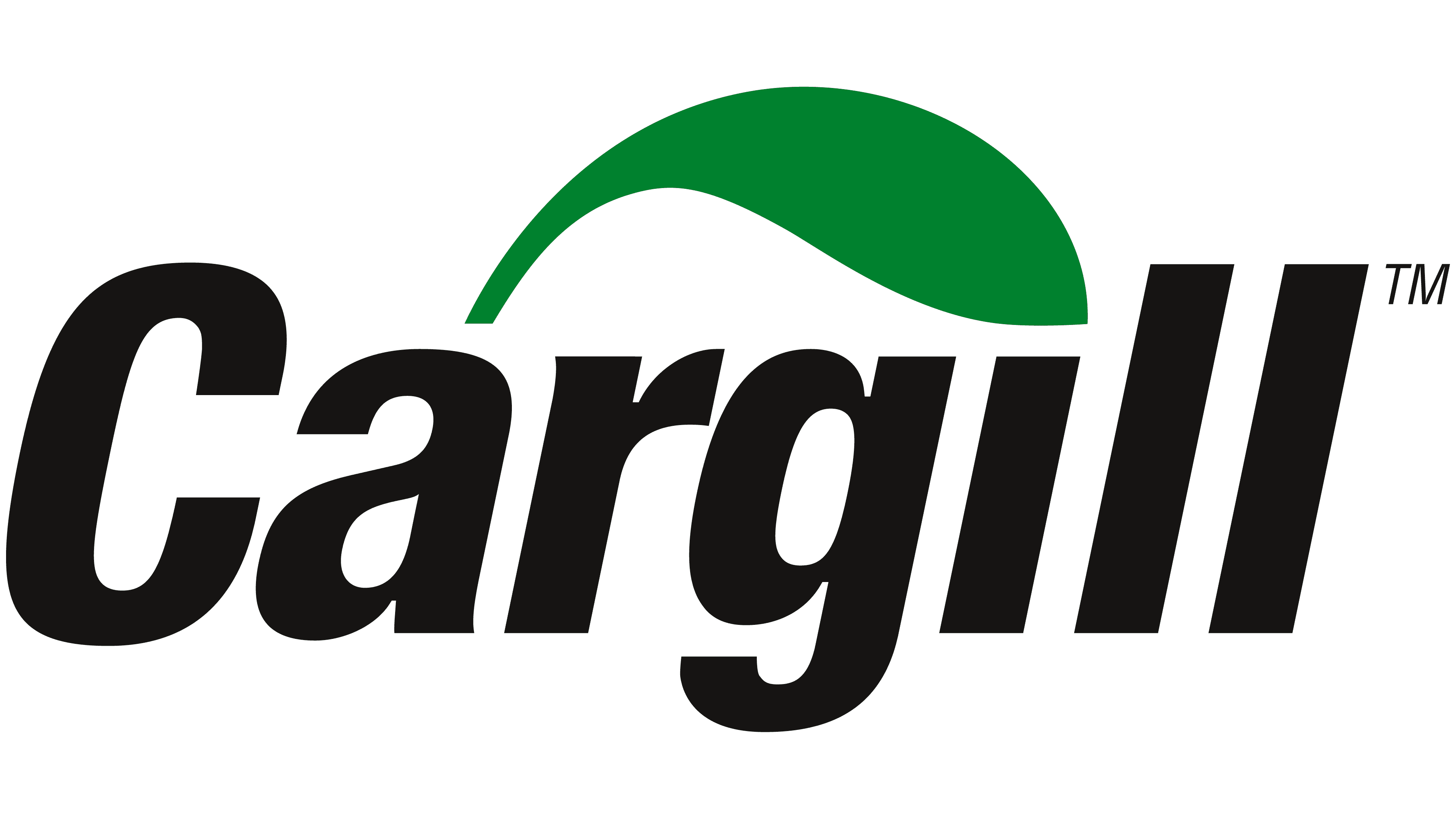
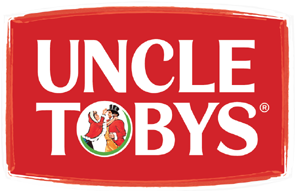
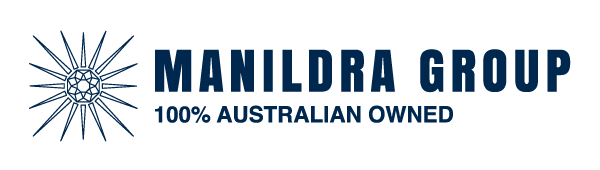
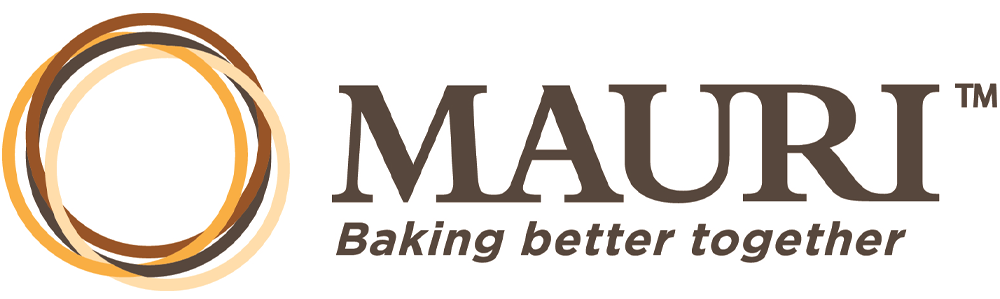
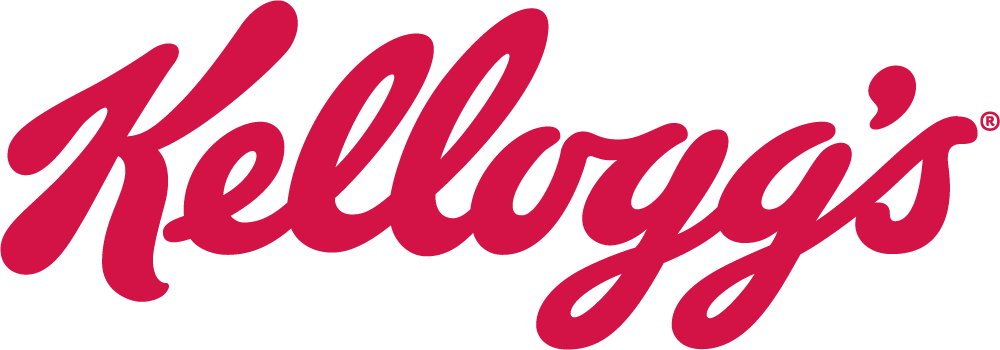
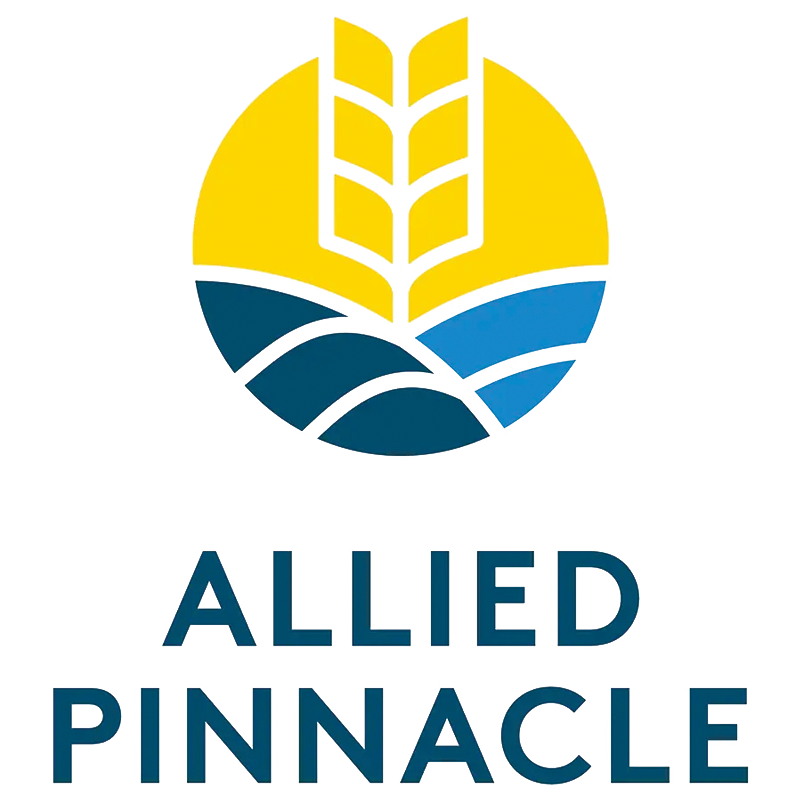
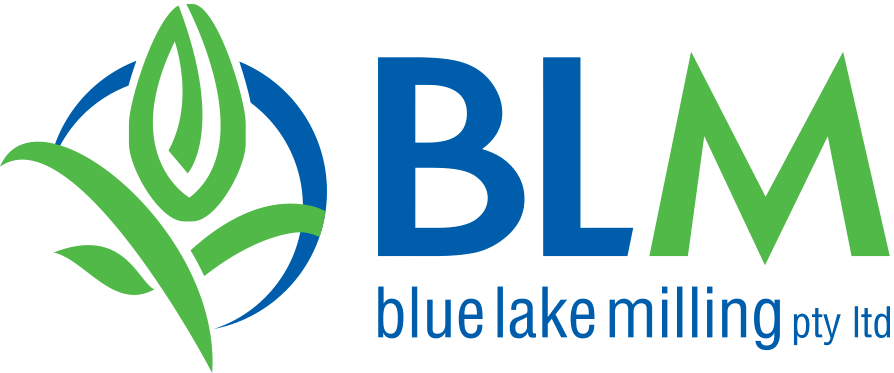
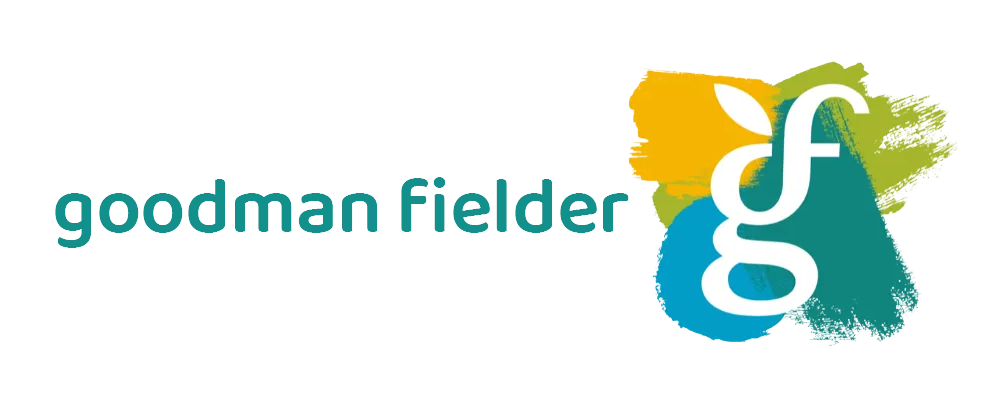
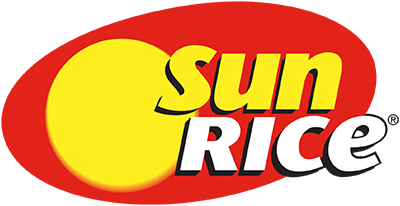
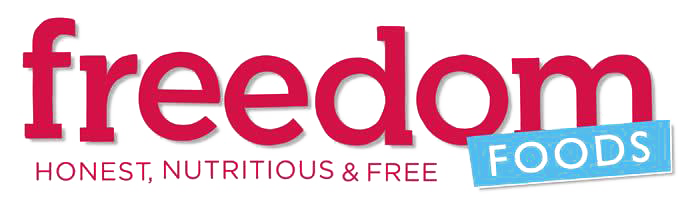
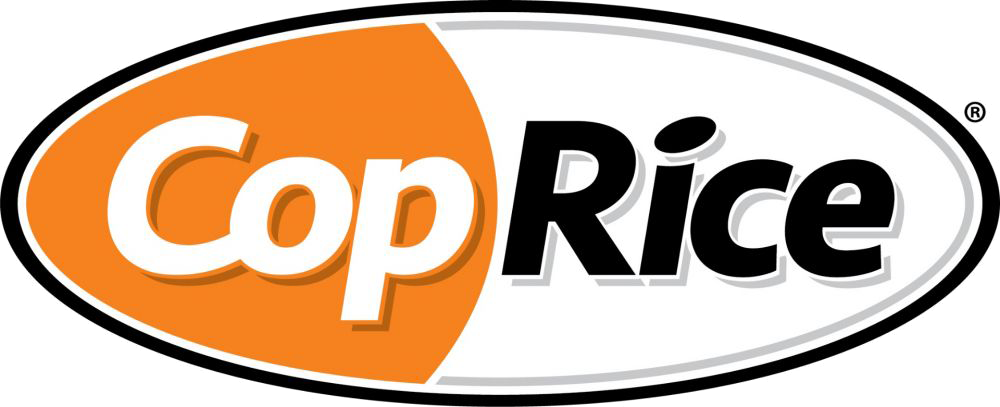
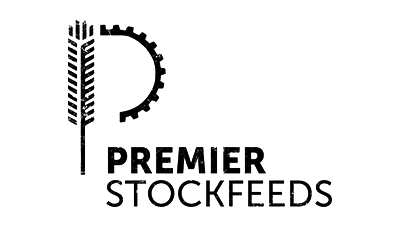
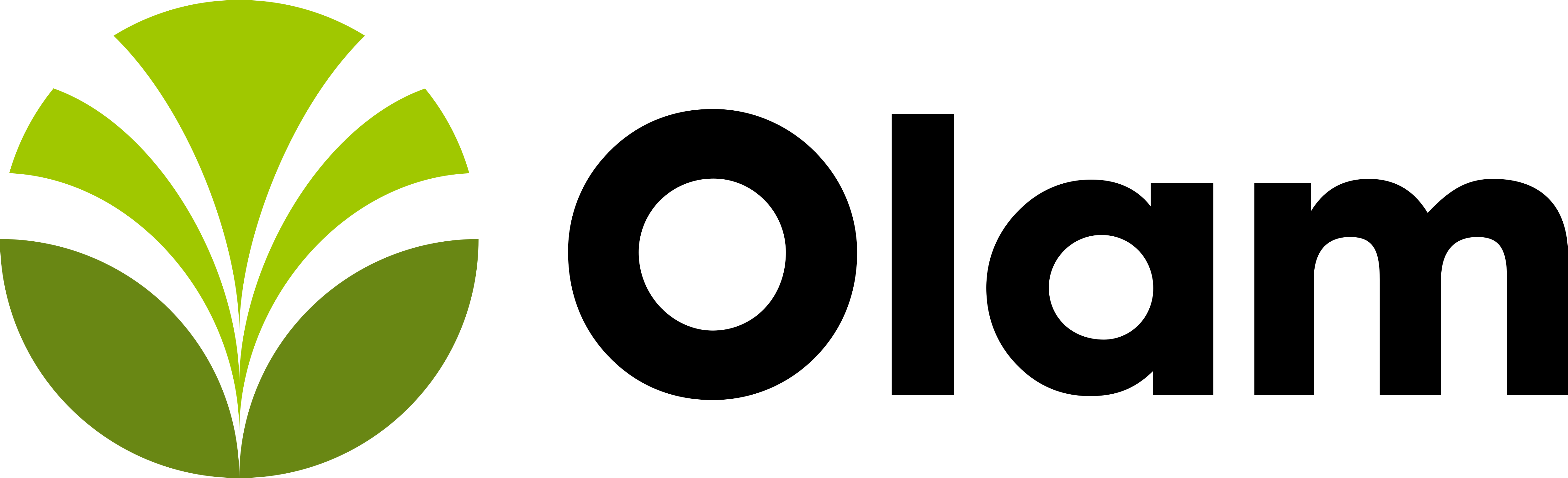
Talk to an Expert
Got a question or need a quote? Our Magnattack experts are here to offer fast, personalized guidance for all your magnetic separation needs. Simply fill out the form below, and one of our specialists will quickly reach out to assist you.