Liquids & Emulsions
In the fast-paced, highly regulated liquid processing industry, product quality and safety are paramount. Magnattack® magnetic separators are engineered specifically to meet the unique demands of beverage production, highly viscous emulsions and slurries, as well as other liquid products, delivering peace of mind, regulatory compliance, and exceptional product purity.
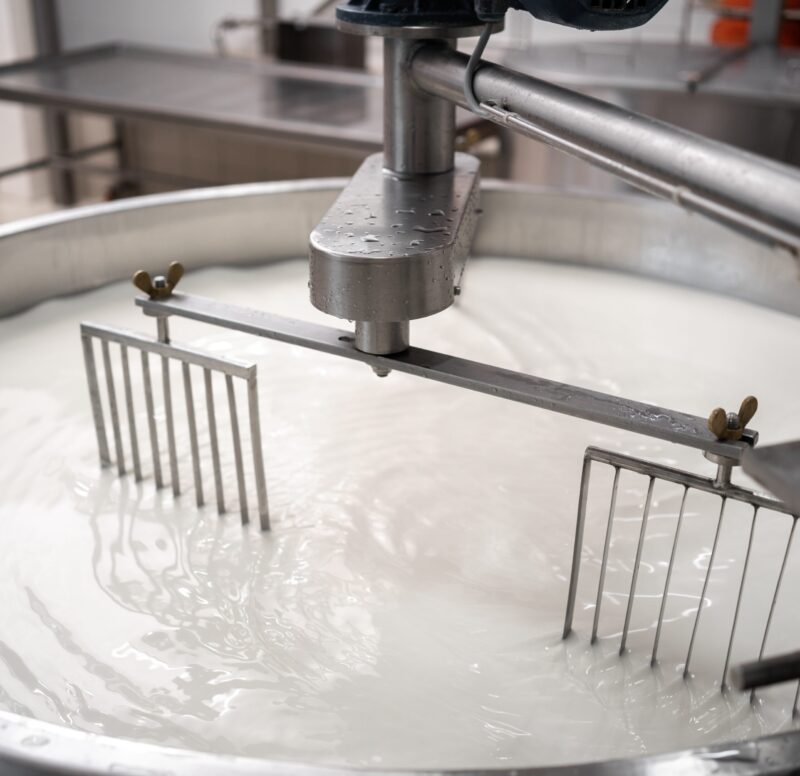
Solutions for Every Stage
of Liquid Processing
Magnattack® magnetic separators offer tailored, high-performance solutions for liquid processing whether juices, sauces, carbonated drinks, wet pet food, or dairy—enhancing safety, efficiency, and product quality. Our separators effectively capture fine metal contaminants like stainless steel fragments and tramp iron, protecting both product integrity and equipment.
Engineered to meet FDA, USDA, and HACCP standards, Magnattack systems ensure regulatory compliance and robust contamination defense. Made from food-grade stainless steel, they’re durable, corrosion-resistant, and easy to maintain, ideal for high-volume processing. Specialized liquid separation systems also support continuous, high-flow operations without compromising efficiency.
With decades of experience serving top brands, Magnattack delivers trusted expertise in contamination control, innovation, and industry support.
Markets we work in:
USDA Acceptance
Magnattack received a USDA Dairy Acceptance Certification in 2015 for special models of the Mag-Ram® Self Cleaning Separator, Rapidclean® Drawer Magnet, Round Pipe Separator, and the Powder Transfer Magnet. In 2019, the Emulsion & Slurry Pipeline Separator also received the USDA Acceptance Certification for use in dairy and sensitive liquid applications, as well as meat and poultry applications.
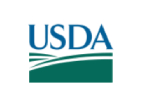
Trusted by Industry Experts
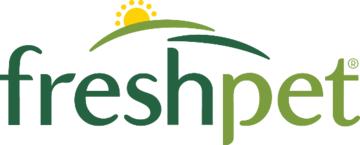
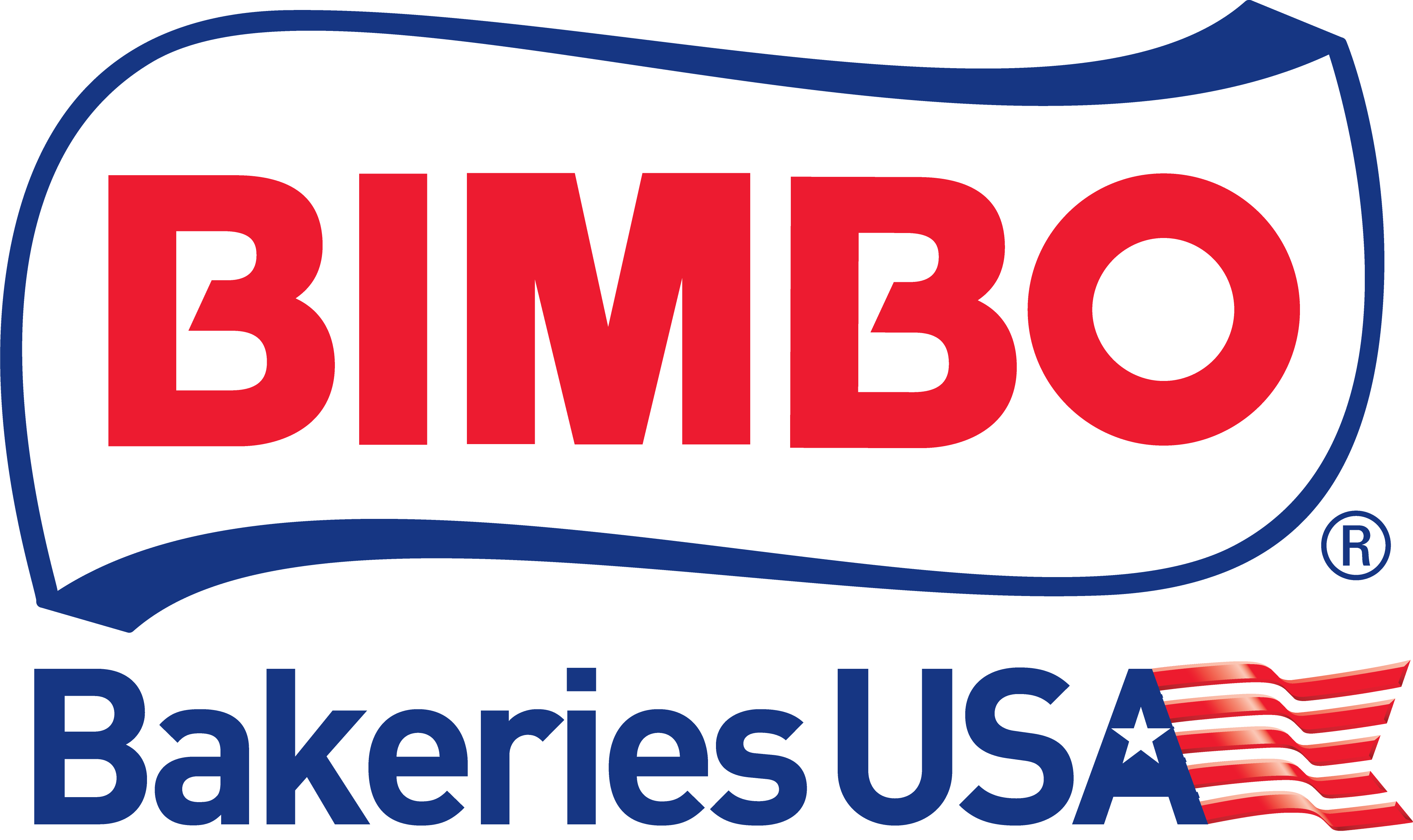
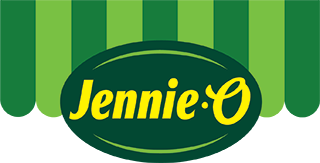
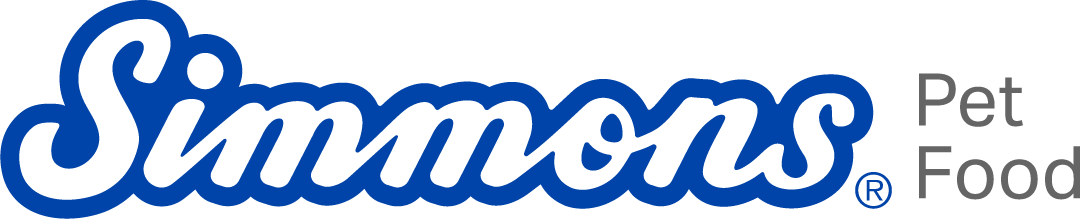
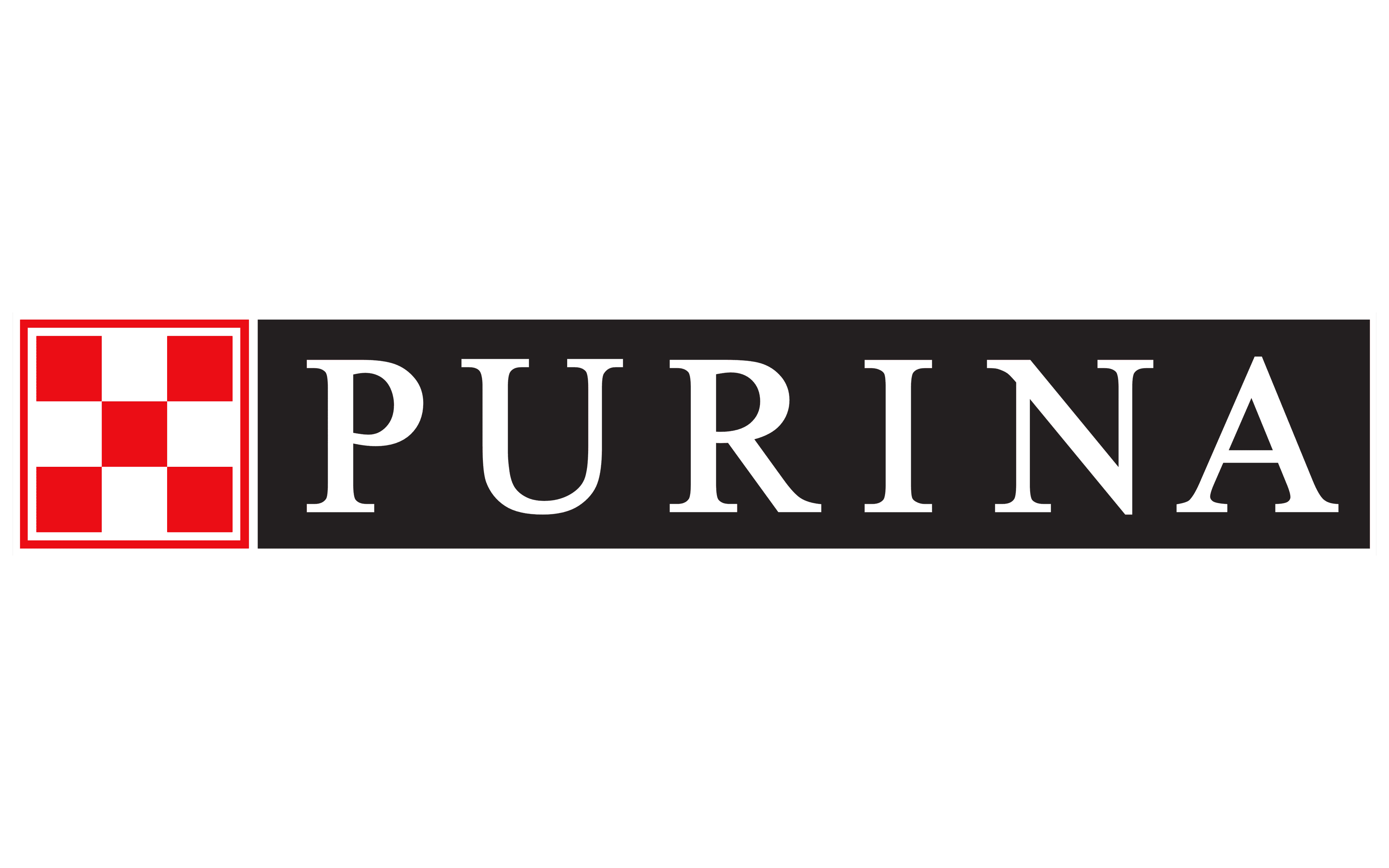
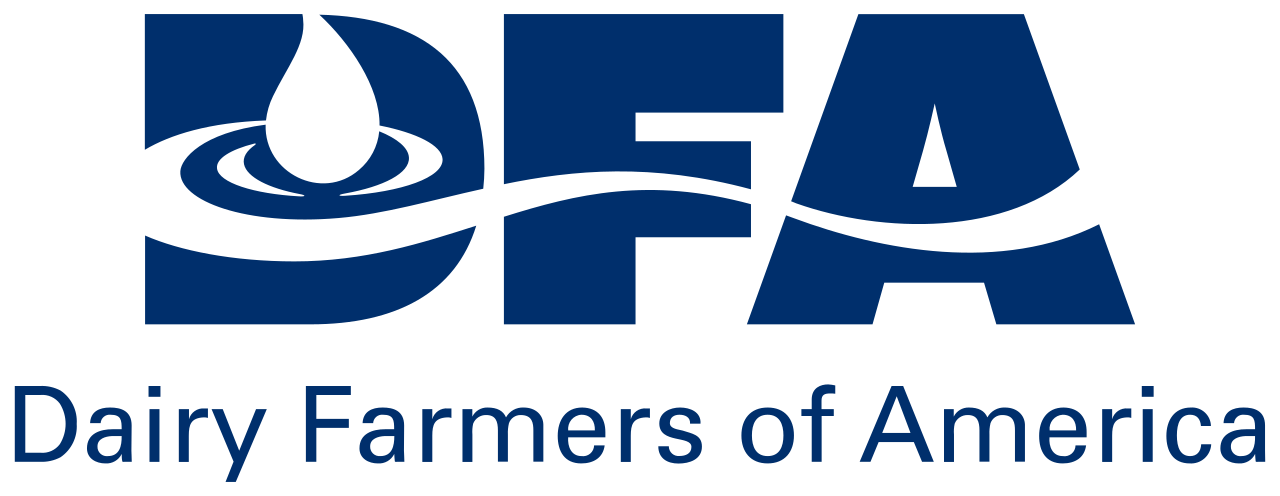
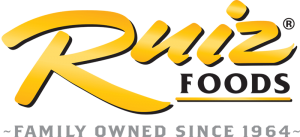
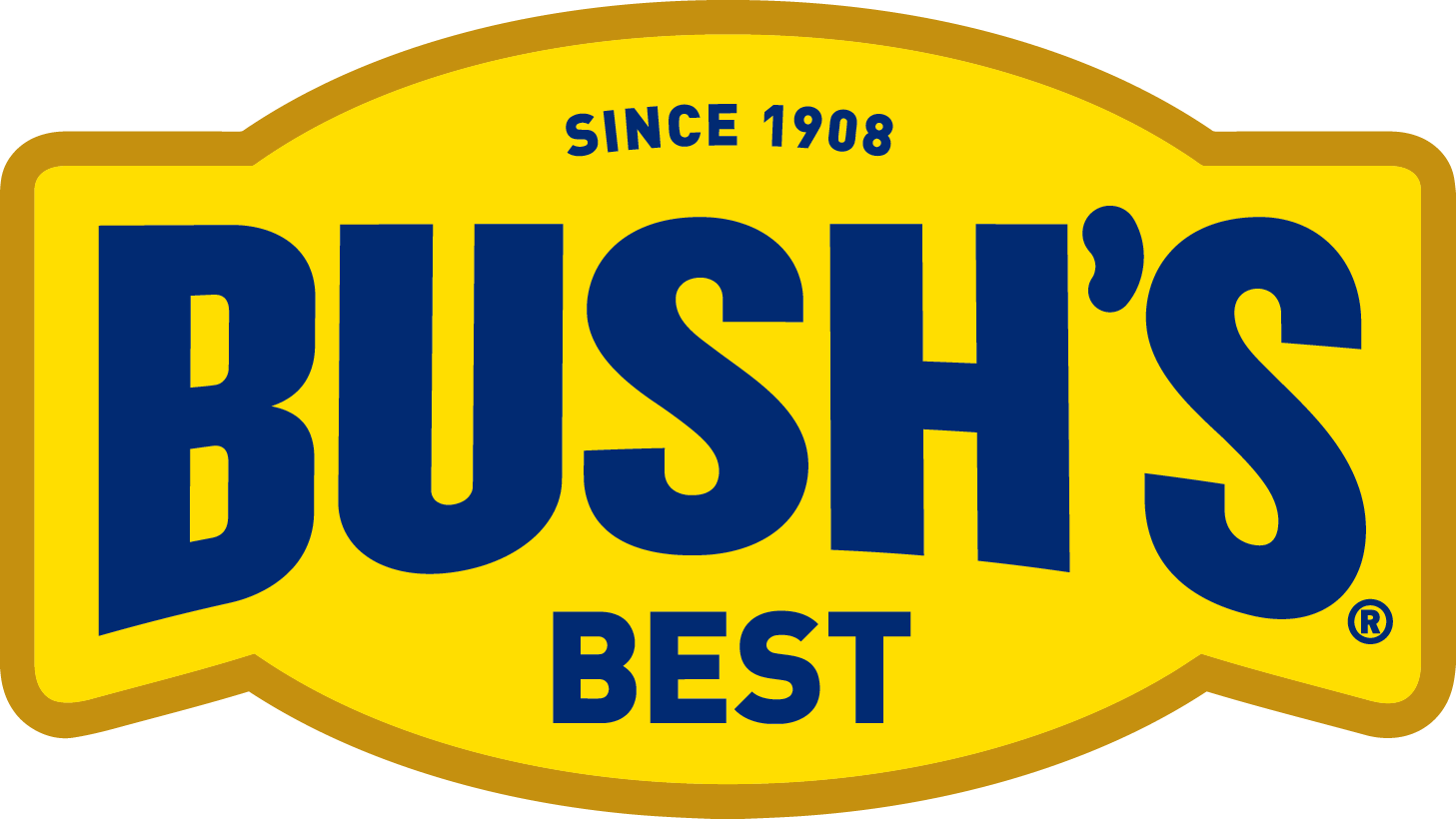
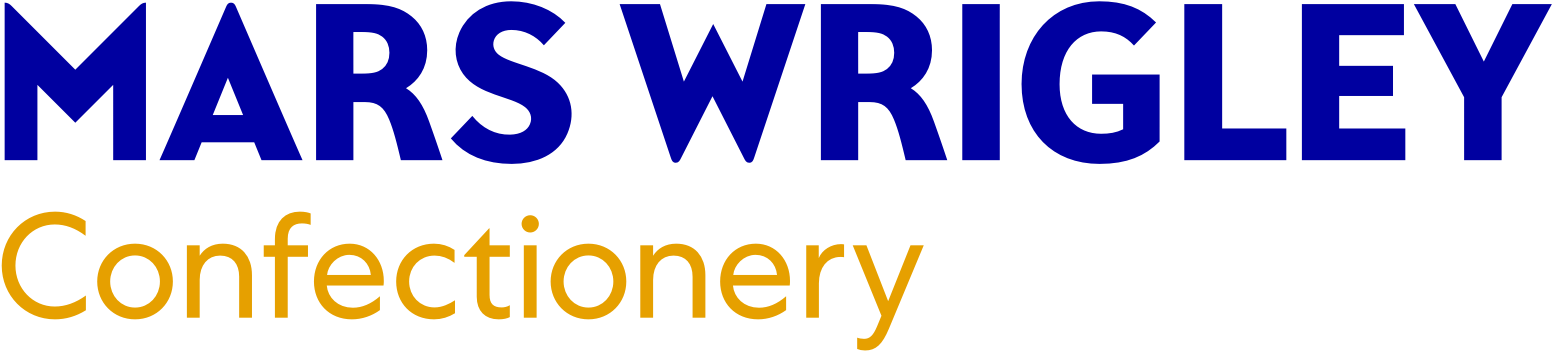
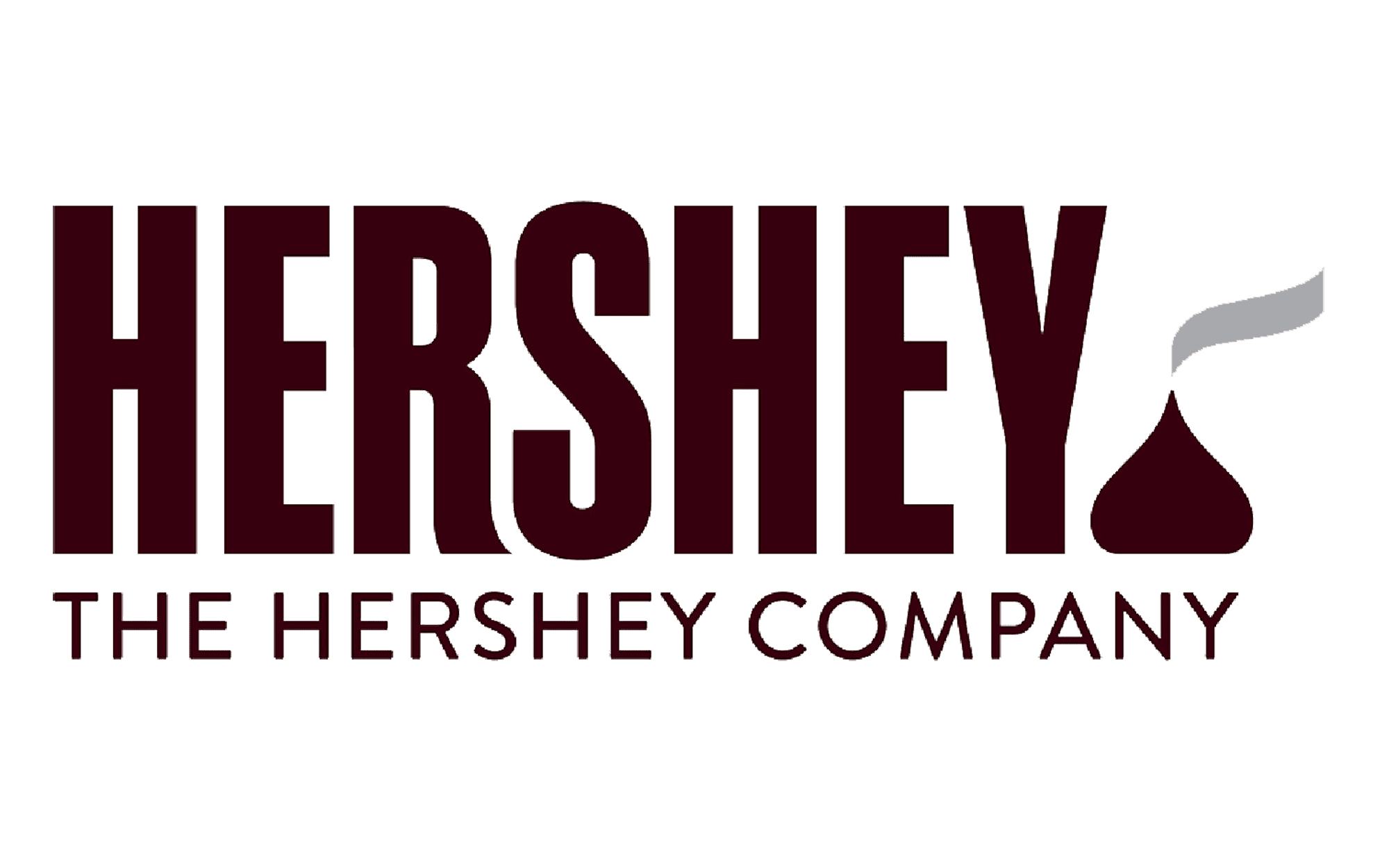
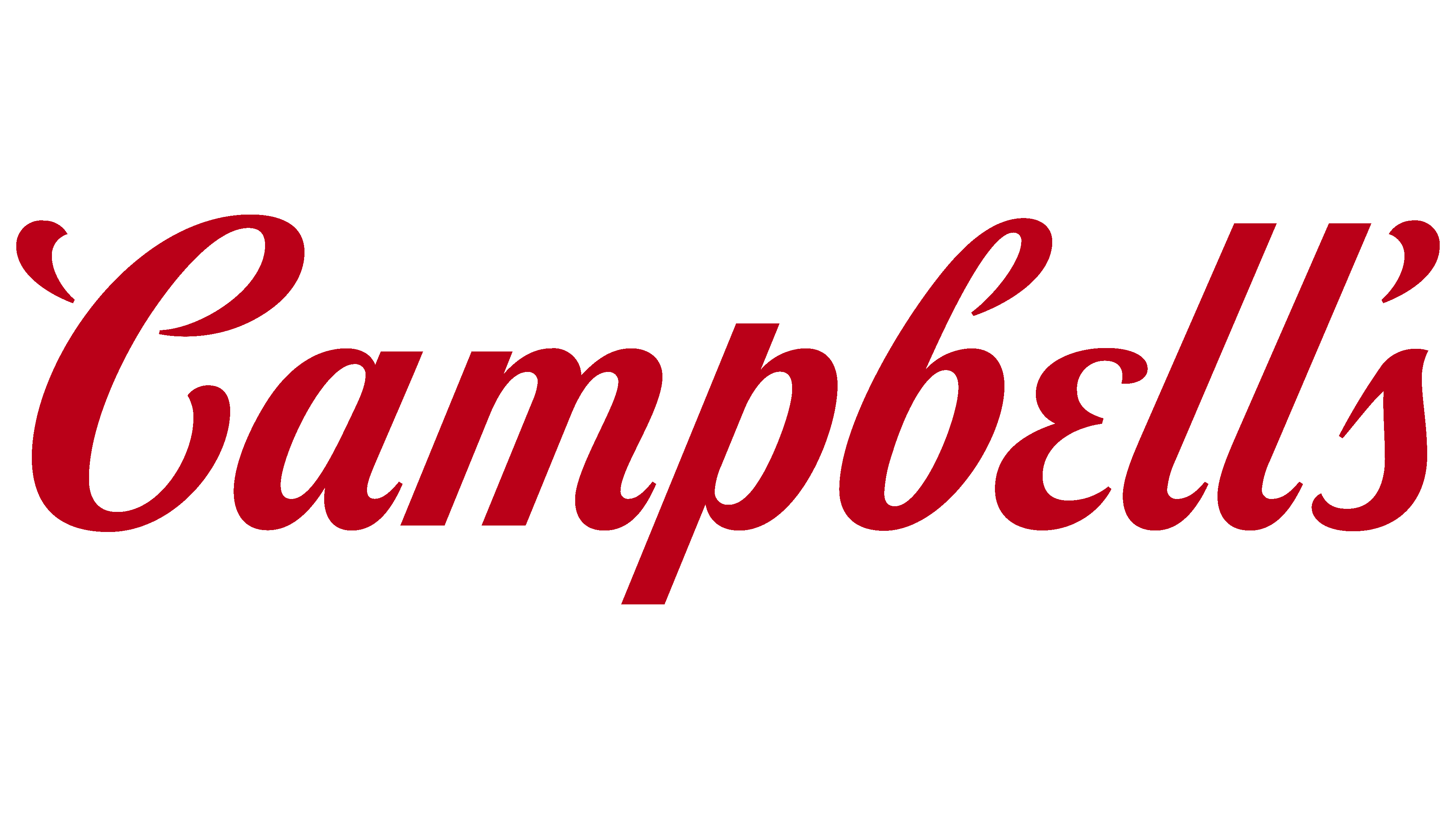
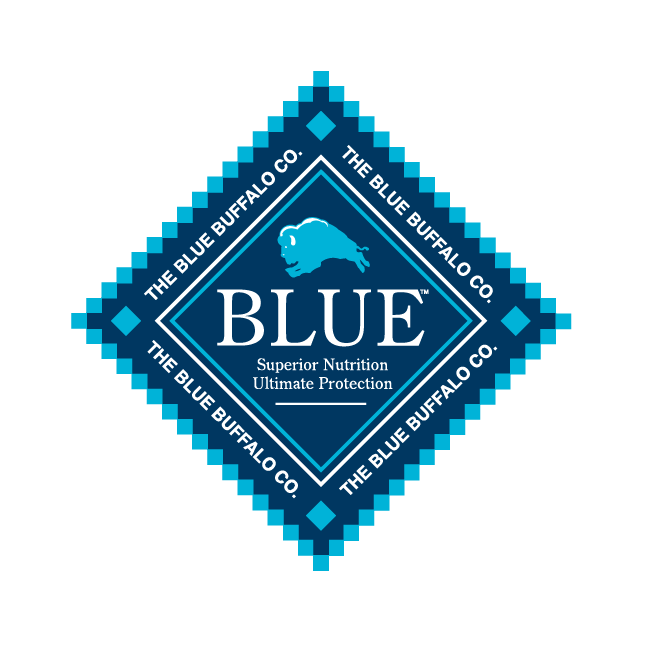
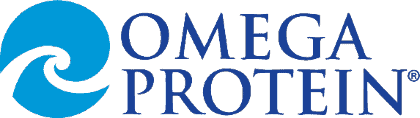
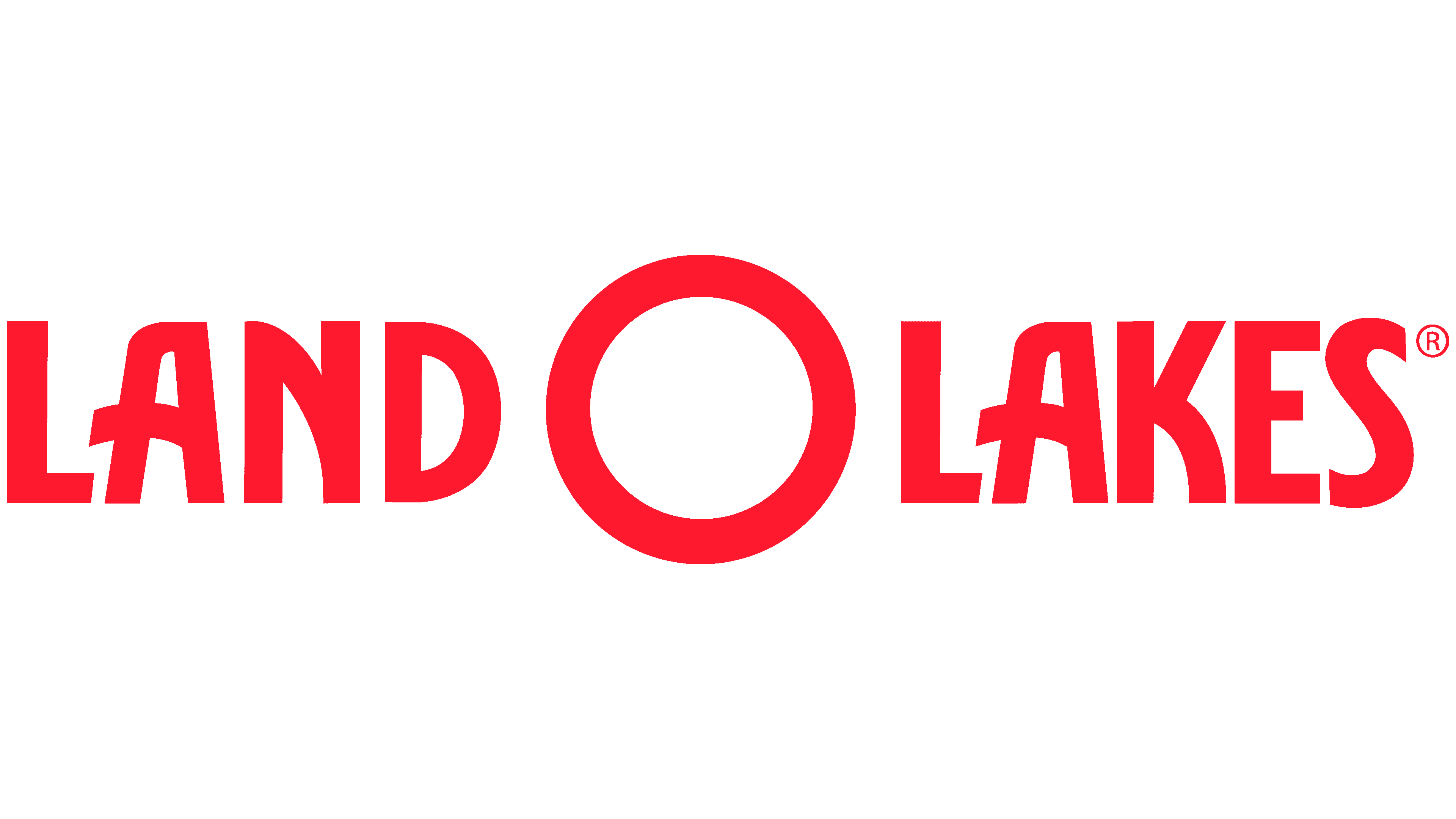
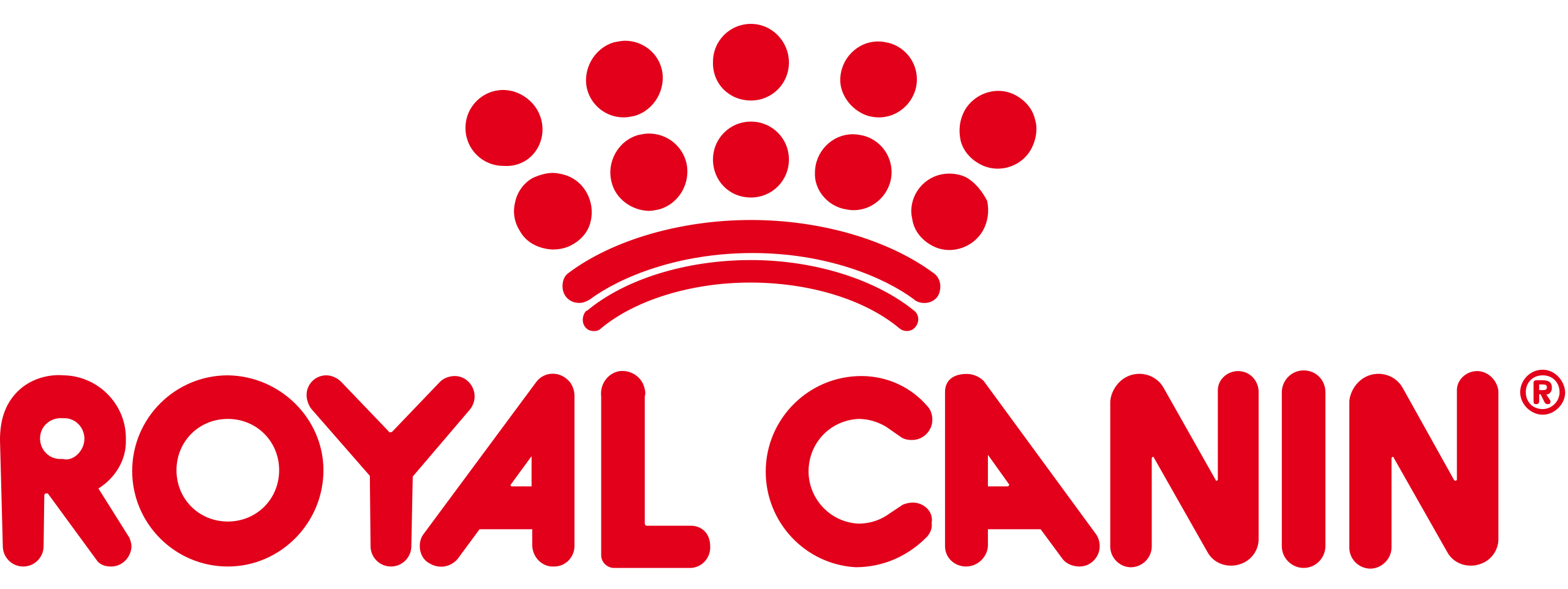
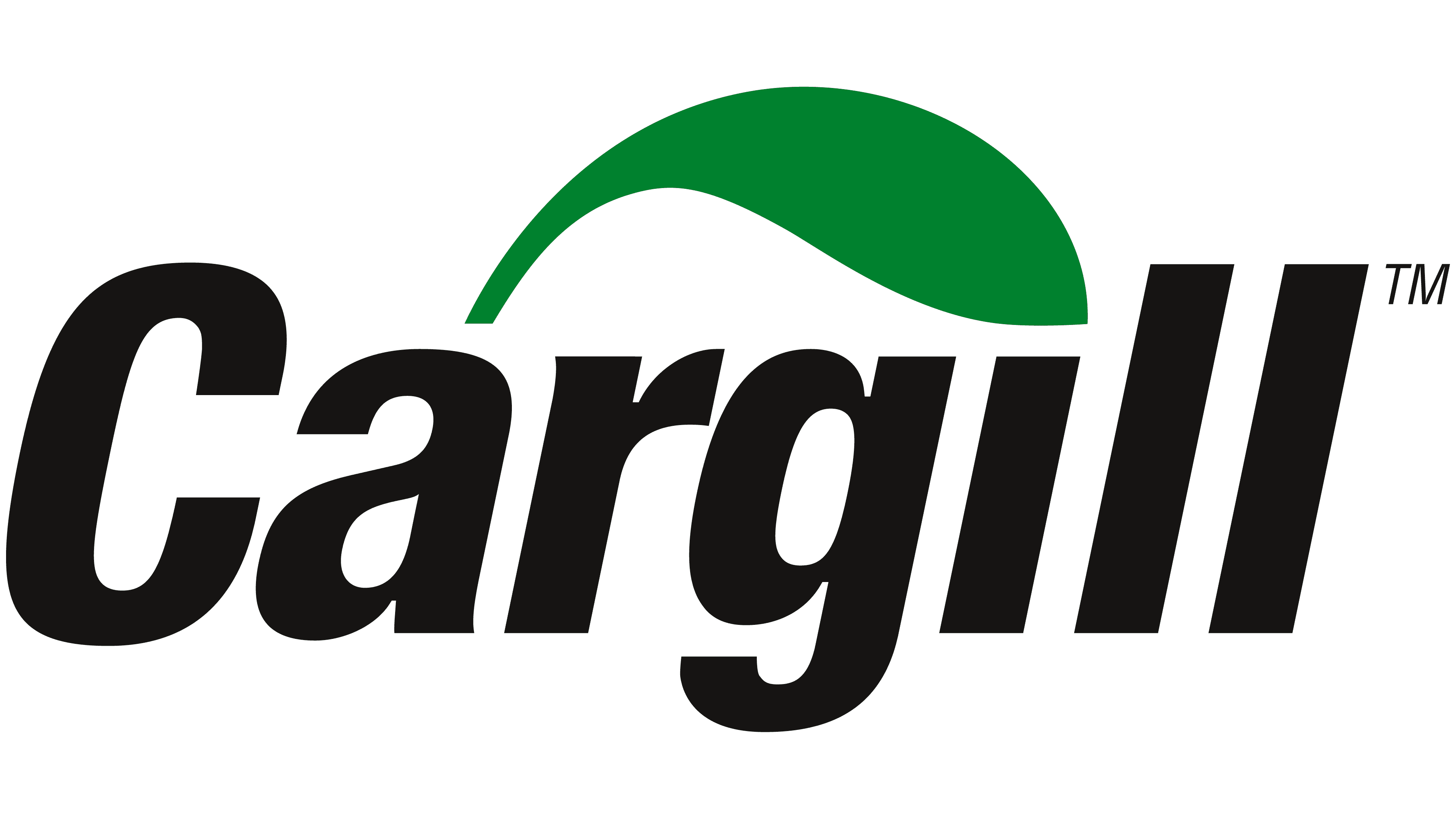
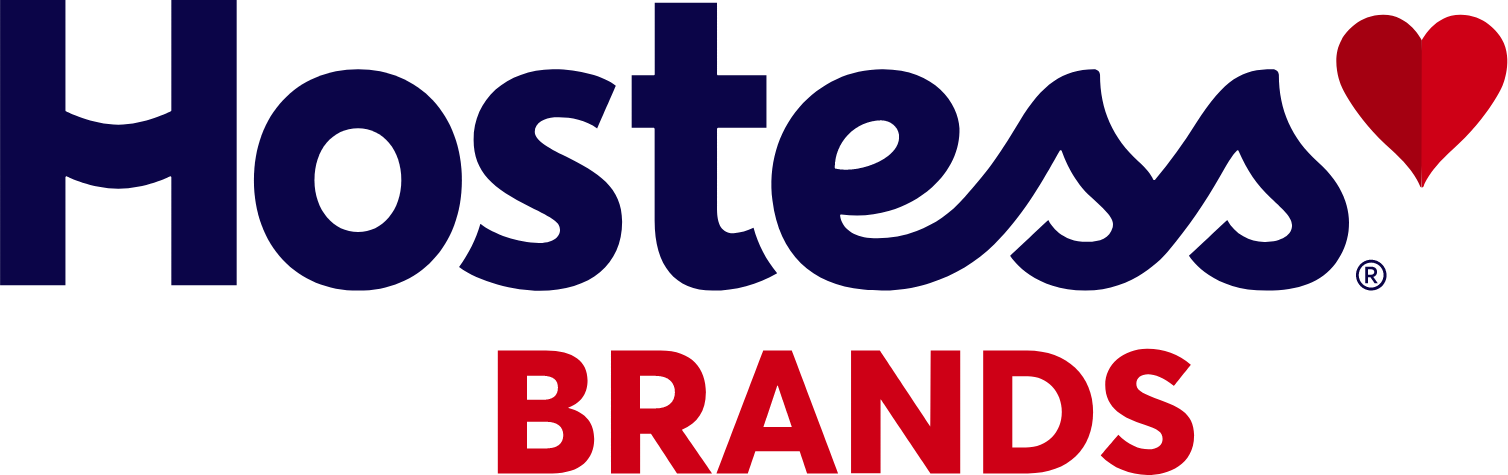
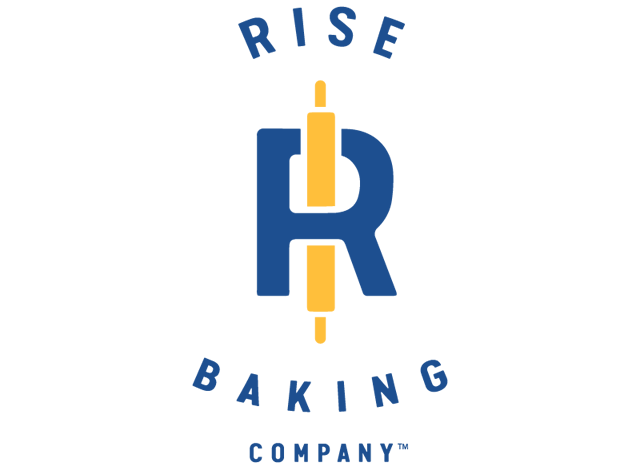
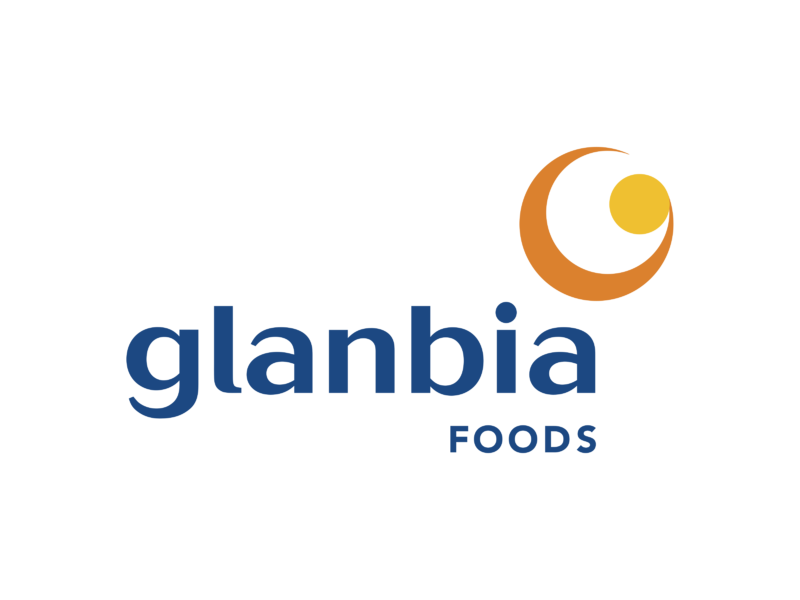
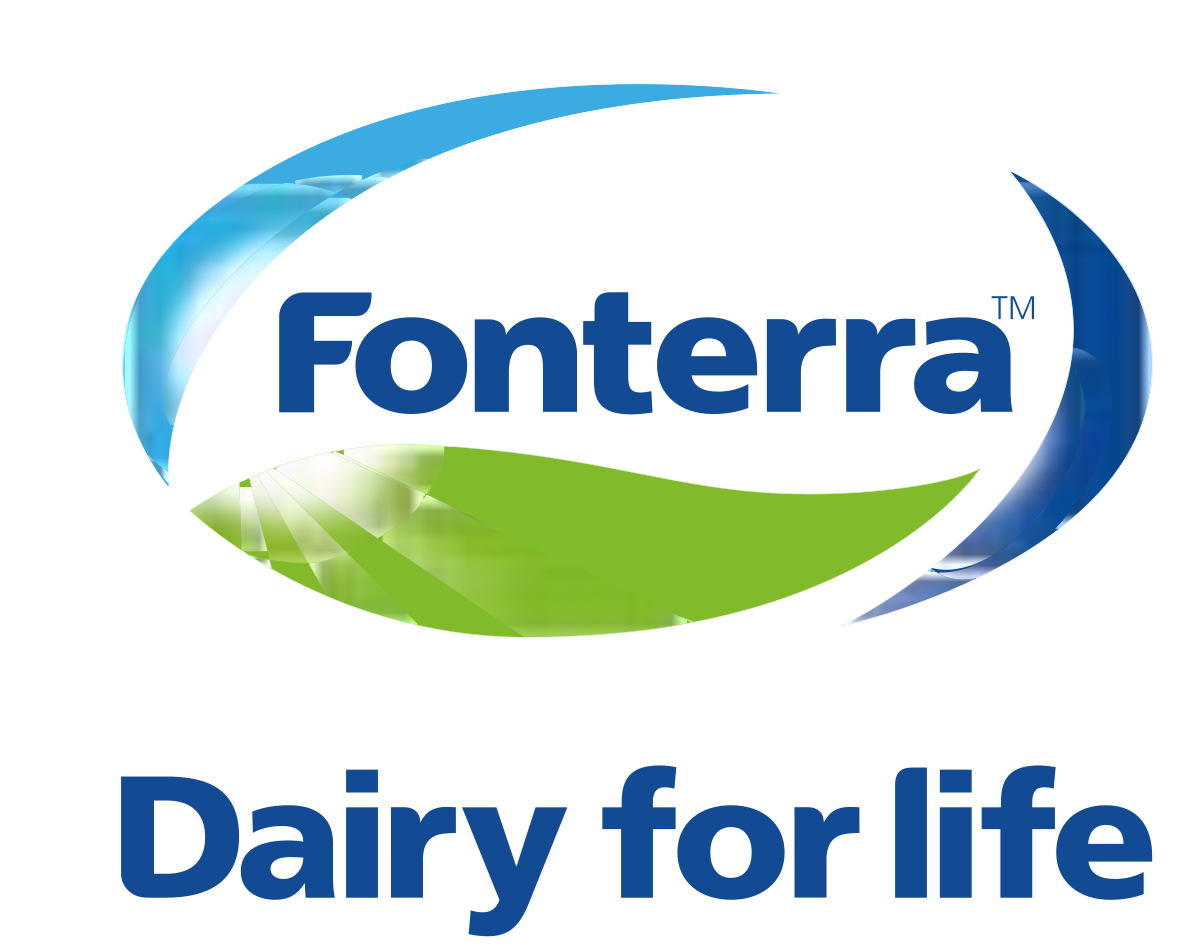
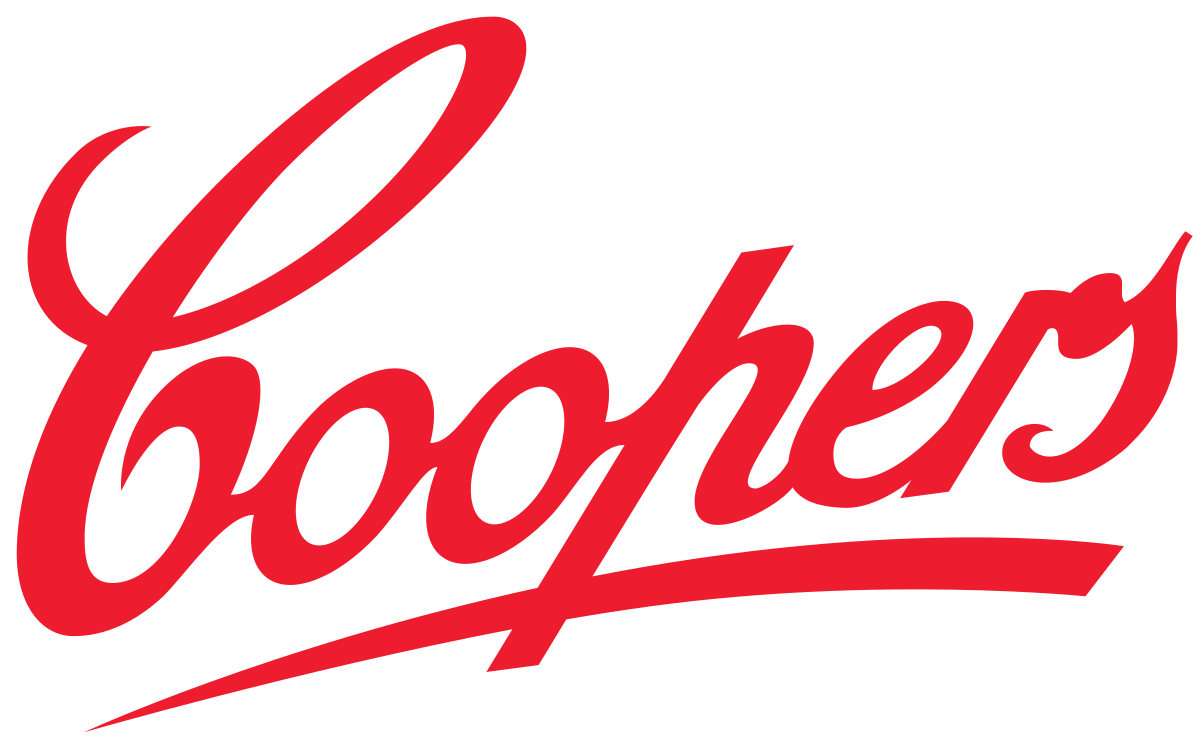
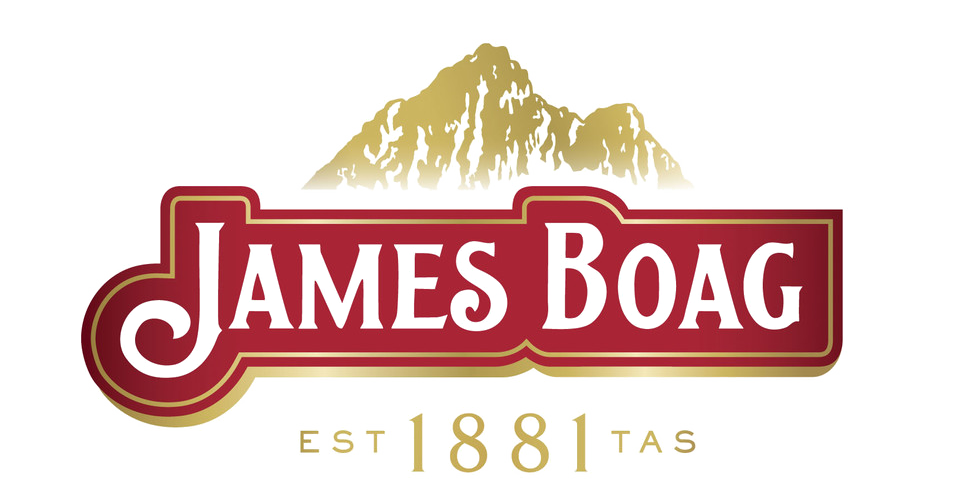
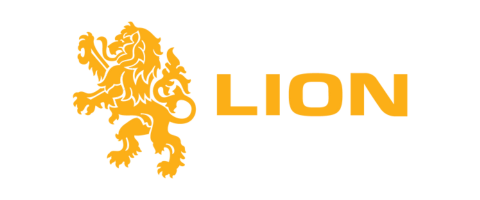
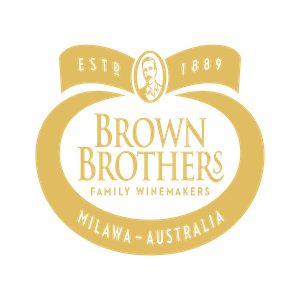
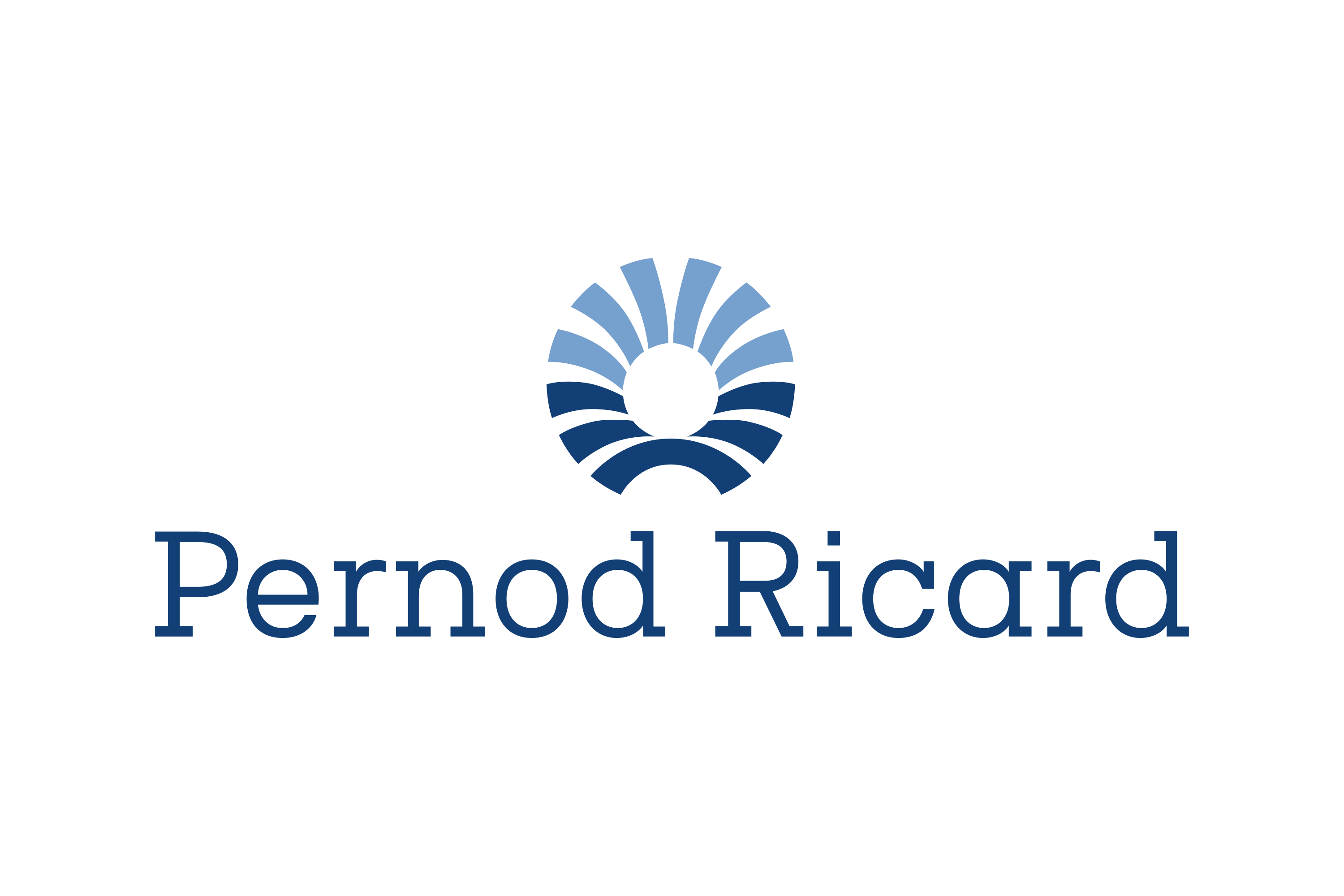
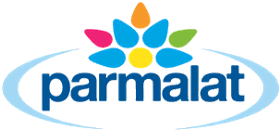
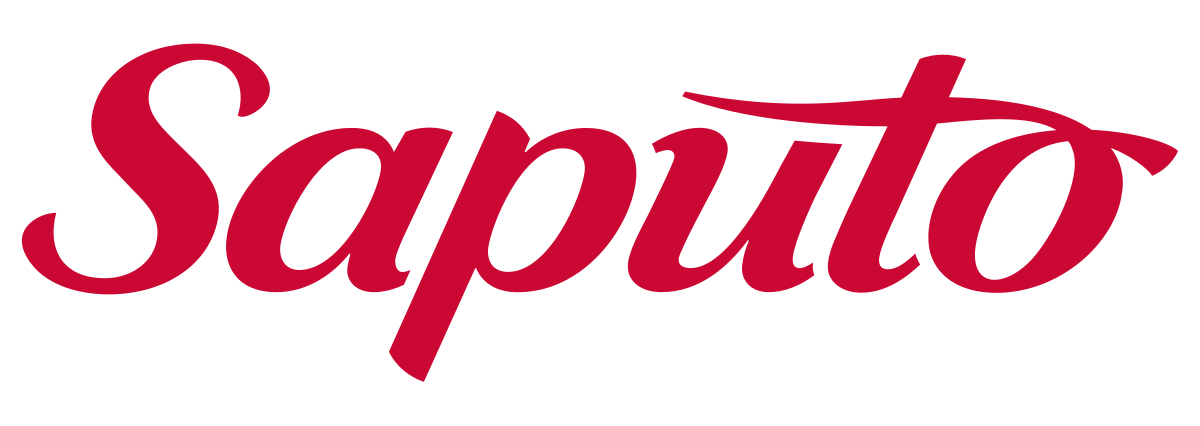
Talk to an Expert
Got a question or need a quote? Our Magnattack experts are here to offer fast, personalized guidance for all your magnetic separation needs. Simply fill out the form below, and one of our specialists will quickly reach out to assist you.