Plant Risk Assessments
At Magnattack®, we understand that proper installation of magnetic separators is critical to protecting your products and your brand. A Plant Risk Assessment is the first step in ensuring that your food processing plant is equipped with the right magnetic solutions for effective contamination control. Our experienced technicians will evaluate your entire process line, identify potential risks, and recommend the most effective magnetic separation systems to prevent metal contamination. Whether you’re installing a new line, upgrading equipment, or optimizing existing systems, a thorough risk assessment can save you time, money, and protect your product quality.
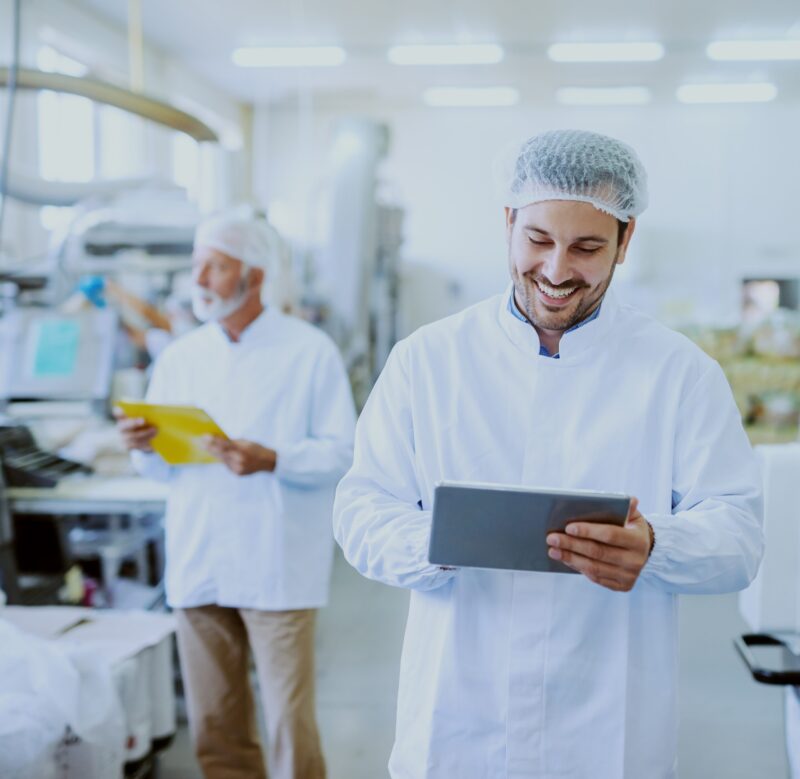
Effective Metal Contamination Control Starts with the Right Magnet Placement: Avoid Costly Mistakes with a Magnattack® Plant Risk Assessment
Installing magnetic separators in a food plant may seem straightforward, but it requires careful planning to ensure effective metal contamination control. Simply choosing a magnet and placing it in the process line may not provide adequate protection. Installing the wrong magnet or placing it incorrectly can lead to costly issues like metal contamination in the final product, potential product recalls, and brand damage.
To help prevent these issues, Magnattack® offers Plant Risk Assessments. To maximize your budget, Magnattack technicians can visit your facility, work closely with your team, and conduct a comprehensive Plant Risk Assessment. This service is particularly beneficial for food processing companies installing a new line, lacking existing magnets, or undergoing plant upgrades. Our technicians will evaluate key factors such as process lines, ingredient entry and exit points, types of ingredients processed, past foreign metal incidents, tonnage rates, and the performance of existing magnets or metal detectors, among other critical elements.
This assessment helps processing companies achieve effective metal contamination control and avoid unnecessary costs.
Brochures
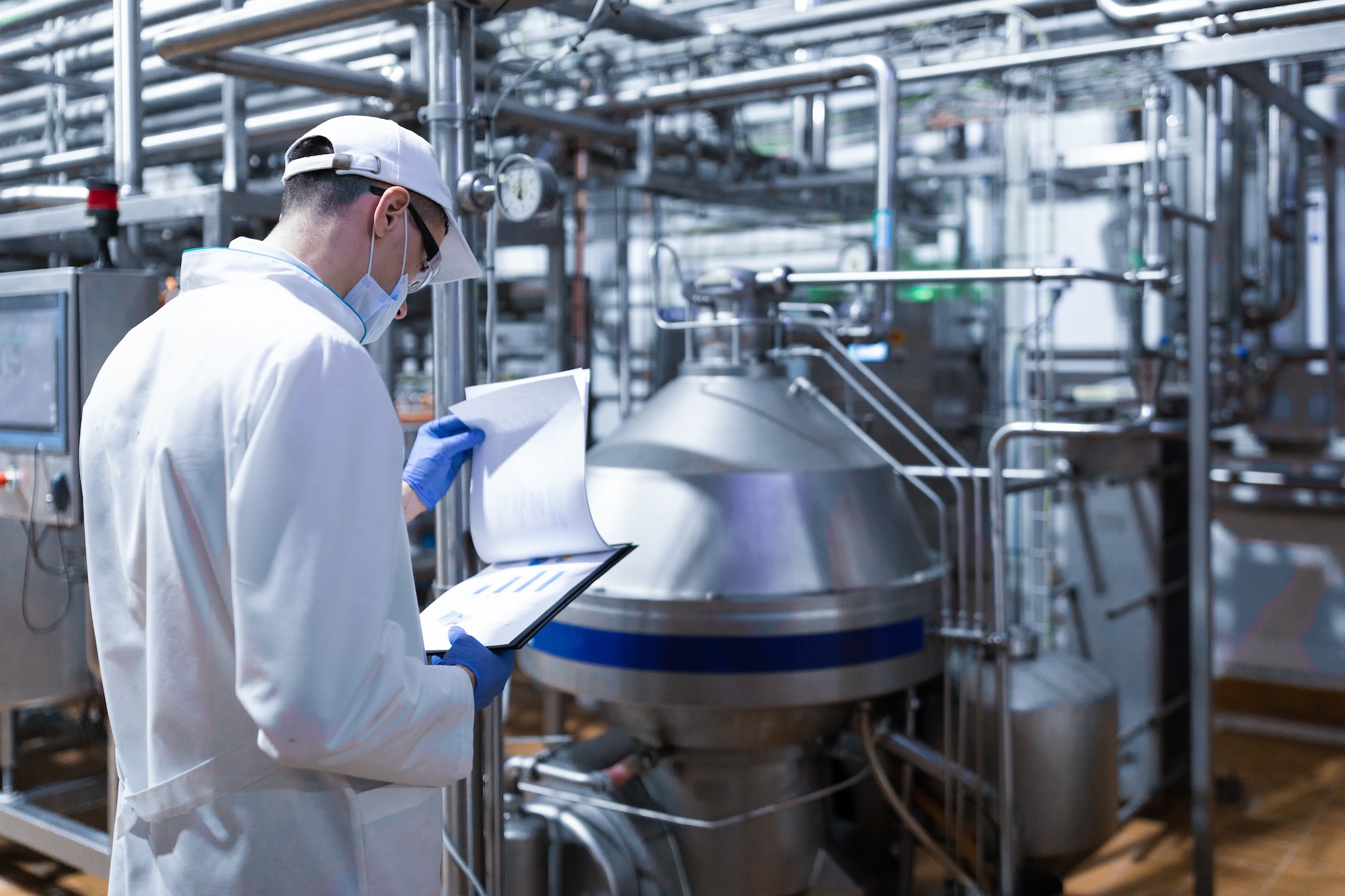
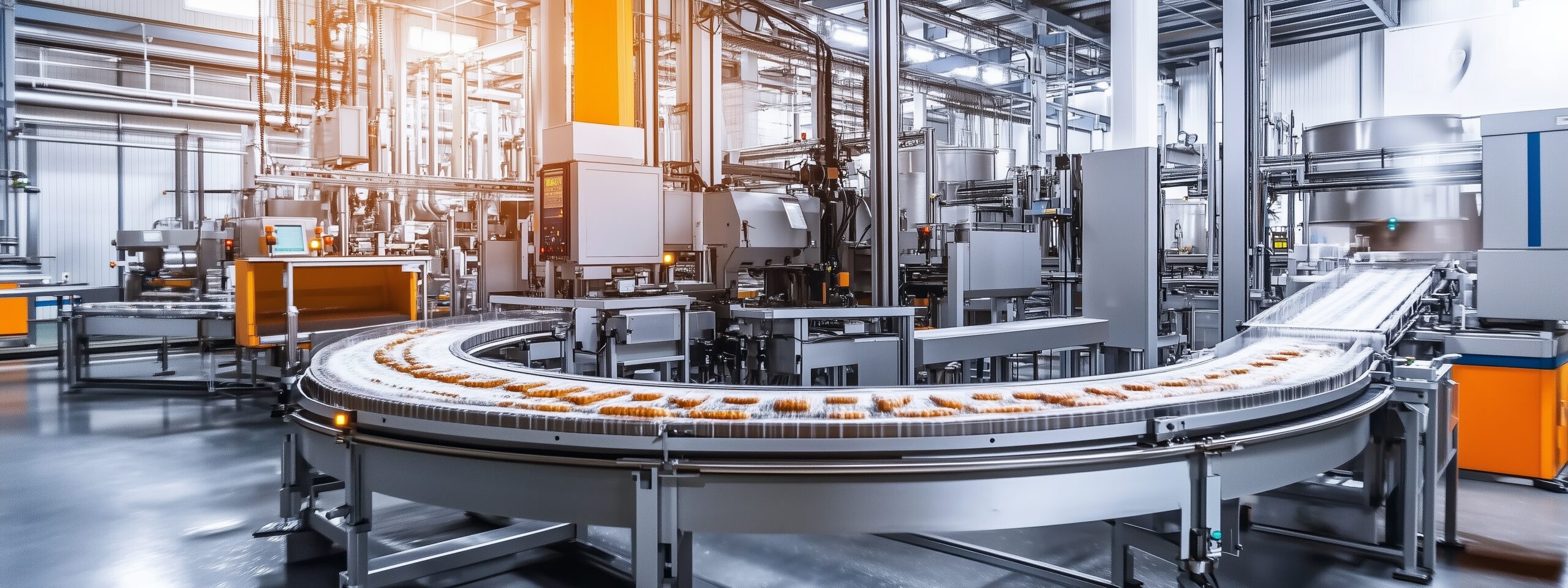
Talk to an Expert
Got a question or need a quote? Our Magnattack experts are here to offer fast, personalized guidance for all your magnetic separation needs. Simply fill out the form below, and one of our specialists will quickly reach out to assist you.