Reducing Downtime & Production Costs By Increasing Metal Fragment Control
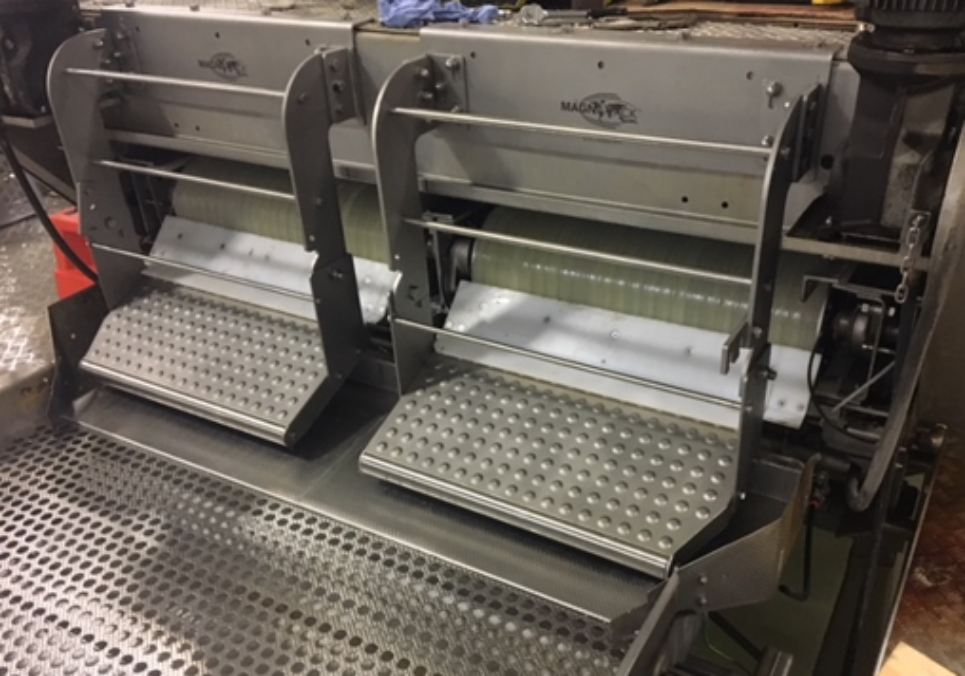
An Australian potato processing facility recently contacted Magnattack® Global with a problem: ferrous metal fragments were increasing their metal detector hits to an unacceptable level and scheduled production time was being lost to downtime and equipment maintenance.
The customer has multiple lines that process 40 tonnes of potato per hour…24 hours, 7 days a week. The finished product is packaged potato, bound for supermarket shelves.
When the customer’s final CCP system (a metal detector) registers a predetermined amount of foreign object matter in the packing area, the production process is halted, and a full investigation of the issue is conducted. These types of shutdowns were occurring, on average, once per day – costing the company thousands of dollars in loss of production and downtime.
Approximate costs of a typical search, investigation, and analysis exercise:
- 2 hours of downtime
- 80 tonnes of potato
- Between $100,000 and $500,000 in loss of production…and a significant accrued impact to their bottom line!
In addition to this, the customer was experiencing damage to their slicers and other processing equipment caused by the presence of metal pieces and magnetic stone.
Solution
After visiting the processing plant and assessing the situation, Magnattack® technicians recommended 2 x custom RE80® Dimple-Mag® Magnetic Extraction Systems.
The Dimple-Mag® systems consist of a specially designed Magnetic Plate paired with a high-intensity RE80® 10-11,000 gauss Magnetic Separation Bar, which offers protection against dislodged fragments and prevents them from re-contaminating the food product.
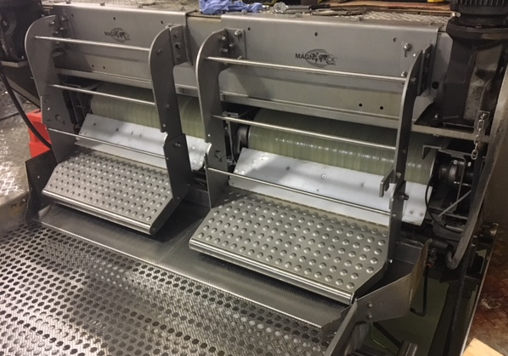
When metal fragments are collected by the Separation Bar, they are washed safely to the underside of the magnet and out of the path of oncoming product.
With the deep field capability of the Plate Magnet added to the intensive coercive force of the Separation Bar, the customer achieved superior control over foreign metal pieces and increased protection against contamination.
The new magnet was installed at a strategic location, before final packing, to efficiently extract foreign metal fragments before they could contaminate final product and trigger a production shut down.
Magnattack® was able to provide an effective solution that not only improved their product purity, but also improved their bottom line!
Results & Achievements
- Reduced metal detector hits
- Reduced frequency of shut down
- Reduced time of investigation
- Reduced product loss
- Reduced magnetic contamination risk at final packing
- Significant ROI
Installing the new Dimple-Mag® systems not only reduced detection hits at the customers final packing area, but it also significantly reduced their investigation area in most shutdown exercises.
In cases where investigations were carried out, they took 30 minutes…only 25% of the time taken before the magnets were installed! This equates to 60 tonnes gained in production, and the magnet paying for itself multiple times in only 1 shutdown.
As a result of what one Magnattack® system could achieve in only one area of the production line, the customer is now looking to further improve their foreign metal controls, with the aim of achieving zero detection hits for magnetic fragments and stone at final packing.
_
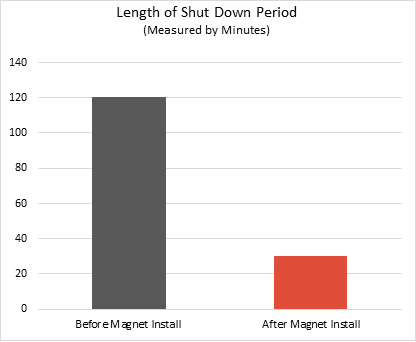
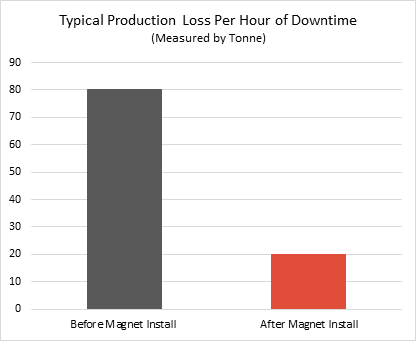
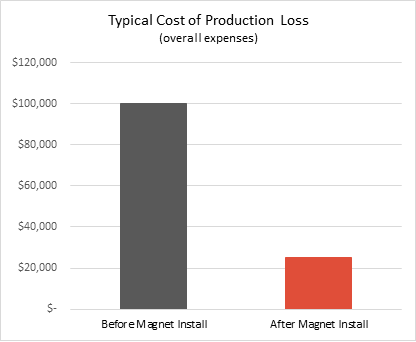
Ready To Reduce Your Costs?
We have 50 years of experience in metal fragment control solutions for the food industry. Our qualified technicians will consider your individual and unique applications to help you select magnetic separators that benefit you and your company!